Building Code Requirements
Building Code Requirements
for Roof Retrofitting
Roof Hugger Sub-Purlins Can Allow Older Metal Buildings to Meet Current Standards
Building Code Requirements
Building Code Requirements for Roof Retrofitting
Roof Hugger Sub-Purlins Can Allow Older Metal Buildings to Meet Current Standards
Compliance with Today’s Strict Building Code Requirements
Today’s stringent building codes call for innovative solutions, especially in retrofit scenarios. Understanding critical elements like wind and snow loads, roof geometry, aesthetics, fire safety, and solar compatibility can help secure a more sustainable, code-compliant, and cost-effective building solution.
Ever wonder why it is necessary to add framing in the corners and the edges of an older metal buildings when reroofing?
It is because of the differences in the Pre-2002 building code and the new building code. Old code buildings have roofs designed with a uniform loads unlike today’s buildings.
disclaimer:
Roof Hugger, LLC is a component manufacturer and as such does not include project engineering with it products. Roof Hugger, LLC has however done extensive testing of its products by independent third party engineering and testing firms and makes that information available for review by design professionals for their exclusive usage.
Users of the provided information which includes but is not limited to system capacities, load tables, cad details, grid assemblies, product specifications, etc., assume full responsibility for all design decisions made relating to the suitability of use. Users must rely on their own judgement or that of a design professional when determining how to best apply the data provided. Users agree that Roof Hugger, LLC is under no obligation to provide additional details, testing or test data on their behalf.
Information regarding systems having received Florida Product Approval is also included. The assembly information for each approval is very specific as to the existing panel, the new panel, the sub-framing system and components used. Deviation from the approved assembly, however slight, will void the approval and necessitate specific project engineering. The use of a Florida Product Approval number is the sole responsibility of the design professional. Roof Hugger, LLC assumes no liability for the incorrect or inappropriate use of these approvals.
Roof Hugger, LLC shall not be responsible for claims, damages, injury or losses to you or third parties arising from your use of the information provided. It is also understood and agreed that any information provided herein cannot be reproduced, duplicated or distributed without the express written permission of Roof Hugger, LLC.
NEED HELP?
Contact us and we will review the current building code in your area and estimate the wind and snow loading requirements. Third-party engineering is available to produce permit drawings and confirm all loads.
Older Building Code Roof Plan (1-1/2:12 Pitch or Less)
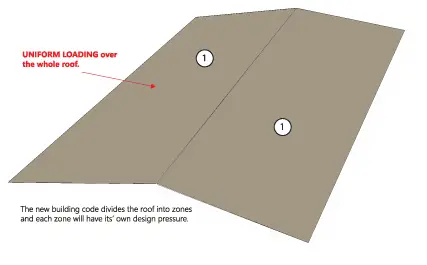
Current IBC 2015/ASCE 7-10 Building Code Roof Wind Zone Plan (1-1/2:12 Roof Pitch or Less), divides the roof into zones and each zone has it’s own design pressure.

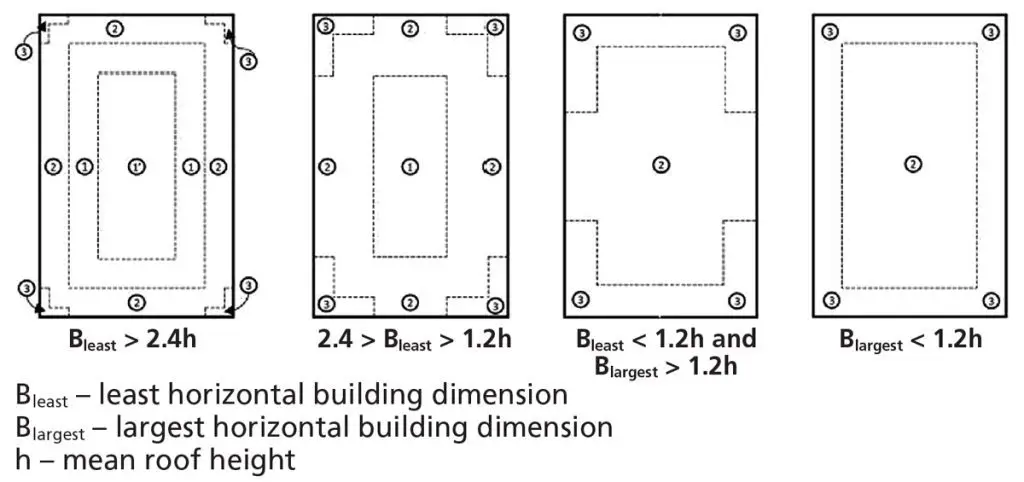
Latest Version of IBC 2018/ASCE 7-16 Building Code Wind Zone Roof Plans
Although not widely adopted at this time, the 2018 IBC will further increase the number of roof zones for Wind and Snow loads.
Roof Hugger has designed corner and edge framing on top of the existing roof panels to reduce the purlin spacing and correctly support the new panels to meet the higher design loads.
By using a combination of structural members running upslope (Sub-Rafters) and parallel to the existing purlins (Sub-Purlins) spaced to provide proper panel support, the proper loading is achieved. Once out of the high load zone we transition back to the easy to install Roof Hugger Sub-Purlins. In many cases where we have tested assemblies, the Sub-Rafters can be made to fit inside the Roof Hugger cutouts lowering the overall framing height and project cost. We call this system “Integral Framing”.

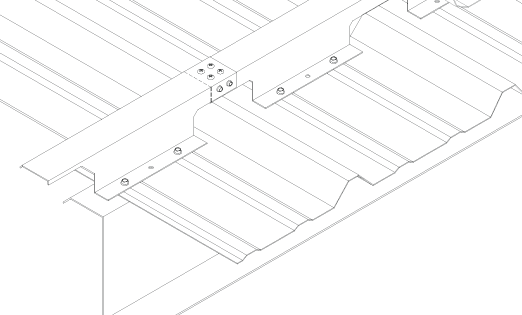
Roof Hugger sub-purlins have the ability to add strength to the existing purlins. This is important because most retrofit systems just add weight.
The drawing shows how the Roof Hugger assembly is secured with our unique attachment system which typically strengthens the existing purlins. Roof Huggers strengthen the purlins allowing them to easily handle the additional retrofit weight.
Roof Hugger is the most tested retrofit sub-framing system available. They are made from high strength 16ga. (0.060 min.), 50 ksi, G-90 galvanized steel
They will allow an existing screw-down metal roof to be upgraded to a standing seam roof without a major engineering analysis and upgrading the existing purlin bracing to make up for the removal of the diaphragm strength provided by the old roof panels.
Crucial Considerations for Building Code Requirements
Tackling Wind, Snow Loads, and Roof Geometry
When contemplating a metal-over-metal retrofit versus a TPO roofing system, it’s vital to understand the challenges presented by snow load, particularly in areas prone to heavy snowfall. The new building codes often raise the minimum ground snow load requirements and necessitate a “drift loading” or “unbalanced loading” analysis due to wind-induced uneven snow distribution on roofs.
TPO systems, composed primarily of foam insulation and a 40-60 mil thick sheet membrane, are not structural components, and they depend on the existing, potentially deteriorated, old metal roof for support. In many cases, the old metal roof fails to meet current snow load requirements on existing purlin spacing, leading to the need for additional framing—an often neglected requirement by single-ply contractors, but not by Roof Hugger.
Furthermore, it’s vital to remember that metal roofs are not designed to accommodate standing water. Single-ply contractors often fill parapet gutters with foam to remedy gutter problems and then install scuppers through the parapet for water runoff. This practice leads to water accumulation on a roof never designed for this load, which can result in catastrophic failures.
checklist for Building Code Requirements
-
Wind Load:
Confirm the TPO system is attached to the structural purlins of the building, not just the roof deck. -
Snow Load:
Verify if the old metal roof can meet current snow load requirements. Consider additional framing if required. -
Roof Geometry:
Ensure the proposed roof solution doesn't encourage standing water, which metal roofs aren't designed for. -
Aesthetics:
Consider the post-retrofit appearance of your building. -
Fire Safety:
Review the fire rating of the new roof post-TPO system installation. -
Insurance:
Check if the new roofing system will impact your building's insurability. -
Solar Compatibility:
Evaluate if the roofing solution is optimal for photovoltaic additions. -
Insulation:
Look for roofing systems that provide not just energy efficiency, but also Above Sheeting Ventilation (ASV). -
Strength:
Consider if the retrofit adds strength to the existing purlins to counterbalance the additional weight of the retrofit system. -
Long-term Value:
Although a new metal roof might cost more upfront, evaluate its long-term benefits including longevity, wind, snow, and insulation code compliance.
Thinking of replacing an old screw-down metal roof with a new standing seam roof?
Consider replacing old screw-down metal roofs with new standing seam roofs, which are modern, versatile, and can solve many issues present in older roofs.